Pliers are an essential tool used across various industries, from construction to automotive repair. If you’re curious about how these tools are made, you’ve come to the right place. This article will walk you through the manufacturing process of pliers, from material selection to the final product. By the end, you’ll understand exactly how manufacturers produce these vital tools and why quality matters so much.
1. What Are Pliers and Why Are They Important?
Pliers are versatile hand tools used for gripping, bending, cutting, and manipulating objects. Whether you’re working on car repairs, plumbing, or electrical tasks, pliers are a must-have. They come in various designs, each tailored to a specific task, such as needle nose, cutting, or combination pliers.
But here’s the kicker—despite their simple appearance, pliers must be designed and made with precision to ensure durability and effectiveness. After all, a poorly made pair can break under pressure, causing potential harm or damage to materials. That’s why pliers manufacturers invest so much in quality control and design expertise.
The importance of high-quality pliers cannot be overstated. These tools are often used in environments where safety is paramount, and subpar tools can result in accidents. When made well, pliers provide a strong grip, which is essential for performing precise tasks without slipping. This makes them reliable across industries like automotive, construction, and home improvement.
As with many other tools, pliers come in various shapes and sizes. Each design has its own specific use, and manufacturers continuously adapt their offerings to meet industry demands. If you’re in the business of manufacturing or distributing pliers, understanding the different types of these tools and their functions can help guide your purchasing decisions.
Here’s the real story—pliers manufacturing is an intricate process, and each stage is critical to producing a durable, effective tool. But what exactly goes into creating these versatile hand tools? Let’s dive deeper into the materials that are commonly used in pliers manufacturing.
Pliers Type | Usage | Example |
---|---|---|
Needle Nose | Precision gripping in tight spaces | Jewelry making, electrical work |
Cutting Pliers | Cutting wires and small materials | Electricians, construction workers |
Combination Pliers | General purpose gripping and cutting | Home improvement, mechanics |
Locking Pliers | Secure grip for heavy-duty tasks | Automotive repair, metalworking |
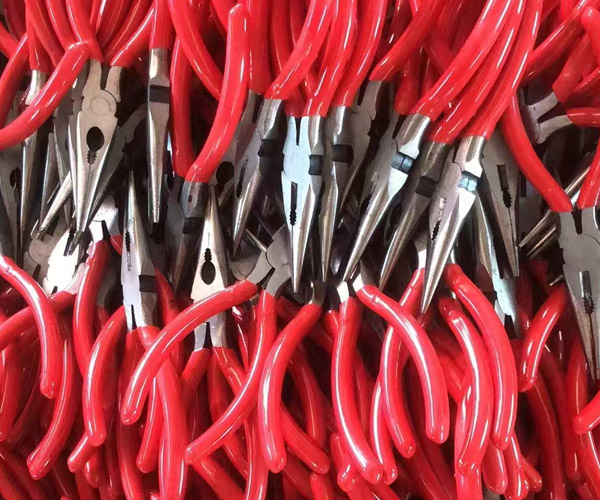
2. What Materials Are Used in Pliers Manufacturing?
When it comes to making pliers, the materials used in their construction play a significant role in determining their durability, performance, and safety. The primary materials used in pliers manufacturing are high-carbon steel, stainless steel, and plastic or rubber for the handles. Each material has its unique set of properties that make it suitable for different types of pliers.
What’s the real story? The steel used in pliers is typically high-carbon steel or stainless steel. High-carbon steel is known for its hardness and ability to hold an edge, making it ideal for cutting tasks. Stainless steel, on the other hand, offers excellent corrosion resistance, which is essential when pliers are used in harsh environments like the automotive or plumbing industries.
Manufacturers also use coatings such as chrome plating to enhance the pliers’ resistance to rust and corrosion. These coatings improve the tool’s longevity, making it a wise investment for users who need reliable tools that can withstand challenging working conditions. Additionally, plastic or rubber handles are often added for comfort and to provide a non-slip grip, ensuring safety and ease of use.
The material selection process is critical because it influences the final quality and performance of the tool. Manufacturers need to consider the intended use, environment, and durability requirements when choosing the right materials for pliers.
Ready for the good part? Let’s take a closer look at how pliers are designed for optimal function.
Material | Properties | Common Uses |
---|---|---|
High-carbon steel | Strong, durable, and sharp | Cutting, gripping |
Stainless steel | Corrosion-resistant and durable | Outdoor, marine, automotive tasks |
Plastic or rubber | Comfortable grip, non-slip properties | Handles for safety and comfort |
3. How Are Pliers Designed?
Pliers are not just made; they are meticulously designed to ensure optimal performance. The design process involves creating a tool that balances functionality, safety, and ease of use. Pliers come in different designs for various uses, and the right design ensures that the tool performs its function effectively.
But here’s the kicker—designing a tool like pliers isn’t as simple as making a few adjustments. There are several key factors that designers have to consider, from ergonomics to the types of materials used. A well-designed pliers handle, for instance, is crucial for comfort, especially for users who rely on these tools for long periods of time.
What sets pliers apart in their design is the balance between the handle length and the gripping mechanism. For example, needle-nose pliers have long, slender jaws that allow users to grip small objects or access tight spaces, while the handles are designed to provide the right amount of leverage. Combination pliers, on the other hand, often have wider jaws for gripping and cutting, and their handles are designed for greater strength.
Designing pliers is a balance between function and comfort. Manufacturers often test their designs with users in mind, conducting ergonomic studies to ensure that their tools are as user-friendly as possible. The right design also takes into account the task at hand. For example, pliers used for electrical work must be insulated to prevent electrical shock, while pliers used for cutting wires must have sharp, precise edges.
Let’s break down the process—pliers manufacturing starts with the design phase, which is crucial for ensuring the right functionality. After design comes the actual manufacturing, which involves shaping and assembling the tool. But what happens during the manufacturing process?
Design Element | Description | Importance |
---|---|---|
Handle Length | Determines leverage and comfort | Affects ease of use and comfort |
Jaw Shape | Defines gripping ability and precision | Crucial for the intended function |
Insulation | Provides protection from electrical shock | Necessary for electrical work |
Grip Material | Determines comfort and non-slip qualities | Enhances user safety and efficiency |
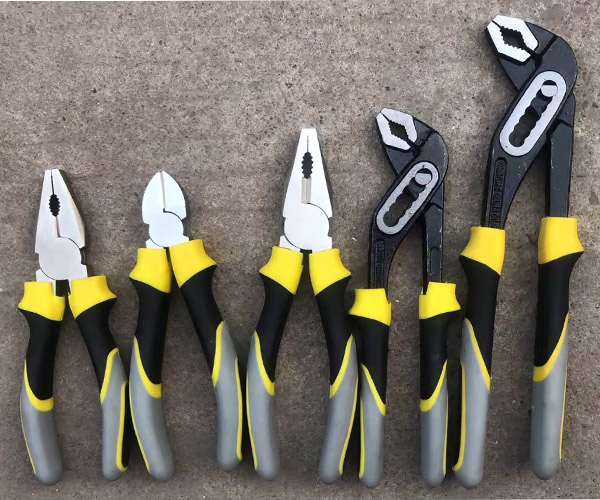
4. What Is the Manufacturing Process for Pliers?
The manufacturing process for pliers is a highly detailed and precise endeavor. From raw material selection to the final product, every step is crucial to ensure the tool meets the required standards of durability and performance.
Ready for the good part? The first step in the manufacturing process is material selection. Manufacturers choose the best steel or alloy for the specific type of pliers they are producing. After selecting the material, the next step is cutting the metal to the appropriate shape. This is done using specialized machines that ensure the correct dimensions for the pliers’ jaws, handles, and other parts.
Once the basic shape is achieved, the pliers undergo a series of heat treatments to improve the hardness and strength of the steel. This is followed by further machining processes, such as grinding and polishing, to achieve the desired finish. For additional durability and aesthetic appeal, pliers may also be coated with a layer of chrome or another protective coating.
Here’s the kicker—every pair of pliers undergoes rigorous quality checks to ensure they meet industry standards. These checks include tests for strength, durability, and functionality. Manufacturers use testing equipment to apply force to the tool to ensure it performs correctly under real-world conditions.
The final step in the manufacturing process is assembly. After all parts are shaped, treated, and tested, the pliers are assembled. This can involve inserting the handles, adding any necessary coatings, and making final adjustments to ensure everything fits together perfectly.
Manufacturing Step | Description | Equipment Used |
---|---|---|
Material Selection | Choosing the right metal for pliers | Raw steel or alloys |
Shaping and Cutting | Cutting the metal into the correct shape | CNC machines, laser cutters |
Heat Treatment | Strengthening the material | Heat treatment ovens |
Polishing and Grinding | Finishing the surface for smoothness | Grinding machines, polishers |
5. How Are Pliers Handled During Production?
The handling of pliers during production is an important factor in ensuring their final quality. From raw materials to the finished product, every stage of production requires careful handling to avoid damage or defects.
This is where it gets interesting—during the production process, pliers are exposed to various forces, such as heat, pressure, and machining. Proper handling of the materials at each stage ensures that the finished pliers are durable and functional. Workers must be trained to handle the tools carefully to avoid introducing imperfections that could affect performance.
For example, when the raw materials are cut, they must be handled with care to avoid any deformation. If the metal is bent or scratched during cutting, it could affect the pliers’ ability to grip or cut properly. Similarly, after heat treatment, pliers are handled carefully to prevent them from being damaged during the cooling process.
But wait, there’s more! The assembly process also requires precision handling. Each part of the pliers must fit together perfectly, and any misalignment could lead to tools that don’t function properly. The final inspection ensures that every pair of pliers meets the required standards before they are shipped to customers.
Handling Stage | Description | Risks/Concerns |
---|---|---|
Material Handling | Ensuring no damage occurs during cutting | Deformation, scratches |
Post-Treatment Handling | Preventing damage during cooling | Cracks or breaks |
Assembly Handling | Ensuring proper alignment of parts | Misalignment or faulty assembly |
6. How Do Manufacturers Ensure Durability in Pliers?
Ensuring durability is one of the most important aspects of pliers manufacturing. A durable pair of pliers can last for years, withstanding tough tasks without wearing down or breaking. Manufacturers use a combination of high-quality materials, advanced manufacturing techniques, and rigorous testing to ensure their pliers are durable.
This is where it gets interesting—durability begins with the materials used. Manufacturers choose high-carbon steel or stainless steel for their strength and ability to hold an edge. After the material is selected, the pliers undergo heat treatment, a process that further strengthens the steel, ensuring it remains tough even under high stress.
Furthermore, coatings such as chrome plating are often applied to protect the pliers from rust and corrosion. These coatings not only improve the lifespan of the pliers but also enhance their aesthetic appeal. This process makes the pliers resistant to wear, ensuring that they can be used for years in various environments, from workshops to construction sites.
Ready for the good part? Manufacturers also test the pliers to ensure they meet strict quality standards. These tests include applying various forces to the pliers to check their strength and ability to perform under pressure. If a pair of pliers passes these tests, it is deemed durable enough for sale.
Durability Factor | Description | Impact on Pliers |
---|---|---|
Material Quality | Choosing high-carbon or stainless steel | Improves strength and longevity |
Heat Treatment | Strengthening the steel through heating | Enhances toughness under pressure |
Protective Coatings | Applying chrome or other coatings | Increases resistance to rust and wear |
7. What Technology Is Used in Pliers Manufacturing?
Technology plays a key role in the modern pliers manufacturing process. From automated machines to precision tools, manufacturers rely on cutting-edge technology to ensure their pliers meet the highest standards of quality and efficiency.
Let’s break it down—one of the most important technologies used in pliers manufacturing is Computer Numerical Control (CNC) machining. CNC machines allow for extremely precise cutting and shaping of pliers parts. These machines are programmed to follow specific instructions, ensuring that every part is made to the correct dimensions.
Another key piece of technology is automated assembly lines. These lines increase efficiency by reducing the amount of manual labor required during the assembly process. They ensure that every part is assembled correctly and consistently.
But here’s the kicker—3D printing is beginning to make an impact on the design phase. Some manufacturers are now using 3D printers to prototype pliers designs before moving to mass production. This technology allows manufacturers to test out different designs and materials without committing to a full production run.
Technology Used | Description | Benefits |
---|---|---|
CNC Machining | Precision cutting and shaping | Ensures exact dimensions and quality |
Automated Assembly | Machines that assemble parts automatically | Increases efficiency and consistency |
3D Printing | Prototyping designs and testing materials | Reduces cost and time for design adjustments |
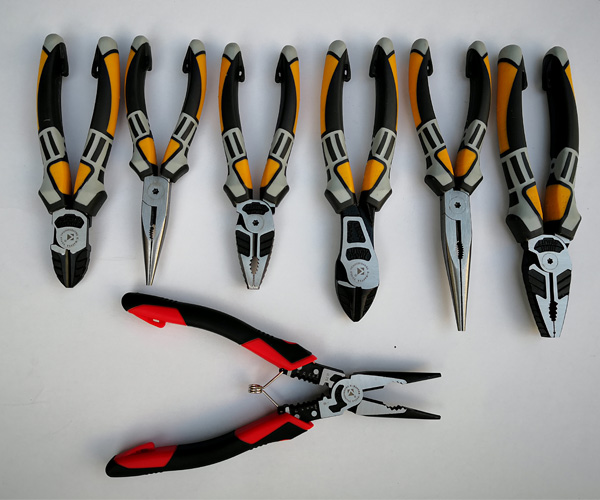
8. What Are the Different Types of Pliers Manufactured?
Pliers come in a wide variety of shapes and sizes, each designed for a specific purpose. Let’s take a closer look at some of the most commonly used types of pliers and their functions.
What’s the real story? Needle-nose pliers are one of the most popular types. Their long, thin jaws allow users to work in tight spaces and grip small objects with precision. These pliers are commonly used in electronics and jewelry making, where small, delicate work is required.
Next up are cutting pliers. These tools are designed with sharp edges for cutting wires and cables. Cutting pliers come in various sizes, with some models designed specifically for cutting through thick materials, while others are intended for more delicate tasks.
Combination pliers are another widely used tool. These versatile pliers feature both gripping jaws and cutting edges, making them ideal for a wide range of tasks. They are perfect for users who need a tool that can perform multiple functions without needing to switch tools constantly.
Pliers Type | Primary Function | Common Uses |
---|---|---|
Needle Nose | Precision gripping in tight spaces | Jewelry making, electronics |
Cutting Pliers | Cutting wires and cables | Electrical work, mechanics |
Combination Pliers | Gripping and cutting simultaneously | Home improvement, construction |
9. How Are Pliers Packaged and Delivered?
Once pliers are manufactured, they must be carefully packaged and delivered to customers. The packaging process ensures that the tools are protected during shipping and that they arrive at their destination in pristine condition.
Here’s the deal—the packaging used for pliers depends on the type of tool and the target market. For mass-market pliers, manufacturers typically use clear plastic packaging that allows customers to inspect the tool before purchase. For higher-end tools or custom orders, manufacturers may use more durable packaging, such as clamshell cases or cardboard boxes with protective inserts.
After packaging, the pliers are ready to be shipped. Manufacturers usually partner with shipping companies to deliver the tools to wholesalers, distributors, or retail outlets. When shipping globally, pliers must be carefully handled to prevent damage, and the packaging must meet international standards for shipping.
Packaging Type | Description | Ideal Use |
---|---|---|
Clear Plastic | Allows customers to view the product | Retail outlets, mass-market tools |
Clamshell Cases | Durable, protective packaging | Premium or custom pliers |
Cardboard Boxes | Sturdy and cost-effective | Bulk shipping, international sales |
10. What Are the Quality Standards for Pliers?
Manufacturers of pliers must adhere to strict quality standards to ensure their products are safe, durable, and effective. These standards are set by both international and industry-specific organizations.
What’s the real story? The quality of pliers is often measured against international standards such as ISO (International Organization for Standardization) or ANSI (American National Standards Institute). These organizations set guidelines for materials, safety, performance, and reliability.
Manufacturers must also pass regular quality control tests during the production process. These tests check for flaws such as cracks, dents, and defects in the handles or jaws. Each pair of pliers is tested for functionality before being approved for sale.
Ready for the good part? Pliers are often tested for things like grip strength, cutting ability, and corrosion resistance. By following these quality standards, manufacturers can ensure their tools perform as expected and meet the needs of customers.
Quality Standard | Description | Testing Criteria |
---|---|---|
ISO Standards | International guidelines for tool quality | Safety, performance, durability |
ANSI Standards | American standards for industrial tools | Grip strength, cutting ability |
In-House Testing | Manufacturer-specific tests | Functionality, defect detection |
11. How Can You Choose the Right Pliers for Your Needs?
Choosing the right pliers can be a bit tricky, especially with the wide range of options available. Whether you’re working on a DIY project or need specialized tools for industrial use, selecting the correct pliers is key to ensuring efficient and safe work.
What’s the real story? The first factor to consider is the task at hand. If you’re working with electrical wires, you’ll need insulated pliers to protect against electrical shock. For cutting tasks, cutting pliers with sharp edges will make your job easier. And if you’re dealing with small, intricate work, needle-nose pliers will give you the precision you need.
Another consideration is the size of the pliers. Larger pliers offer more leverage, making them ideal for heavy-duty tasks like gripping large pipes or removing bolts. Smaller pliers, on the other hand, are perfect for more delicate tasks like jewelry making or small electronics repairs.
Grip comfort is also a big deal—ergonomic handles can make a huge difference, especially for people who use pliers frequently. Manufacturers design handles with rubber or plastic coatings to ensure a firm, comfortable grip that reduces hand strain.
What’s the kicker? When selecting pliers, always choose based on the task and the level of durability required. Whether you’re in construction, automotive, or home repair, having the right pair of pliers is essential for getting the job done right.
Pliers Type | Best For | Features |
---|---|---|
Insulated Pliers | Electrical work | Protection from electrical shock |
Cutting Pliers | Cutting wires or cables | Sharp edges for precision cutting |
Needle Nose Pliers | Precision work in tight spaces | Long jaws for intricate tasks |
Ergonomic Pliers | Extended use | Comfortable, non-slip grips |
12. What Is the Role of OEM Services in Pliers Manufacturing?
OEM, or Original Equipment Manufacturer, services are a critical aspect of pliers production, particularly for businesses that need custom tools to meet specific needs or branding requirements. OEM services allow manufacturers to create pliers that are tailored to the client’s specifications, from custom designs to logo placement.
But here’s the kicker—OEM services go beyond simple customization. They also provide a way for businesses to ensure that their tools meet specific standards for performance and quality. OEM manufacturers work closely with their clients to create pliers that are suited to their unique tasks, such as producing tools with specialized coatings, handles, or jaw shapes.
What sets OEM services apart is the level of customization available. Whether you need pliers with a particular jaw shape, handle material, or a special feature like locking mechanisms, an OEM manufacturer can make it happen. This is especially useful for companies that need tools for niche industries or specific tasks.
Ready for the good part? The benefits of working with an OEM manufacturer extend beyond just product customization. With an OEM, you can also ensure that your tools are produced in large quantities to meet demand while maintaining high-quality standards. Plus, OEM manufacturers are experts in the design and production of pliers, ensuring that the final product is durable, reliable, and cost-effective.
OEM Service Benefit | Description | Example |
---|---|---|
Custom Design | Tailored to specific needs and tasks | Custom pliers for automotive repair |
Branding | Placing logos or branding on pliers | Private label pliers |
Performance Standards | Ensuring tools meet specific standards | High-performance pliers for electronics |
Production Capacity | Ability to produce large quantities | Mass production for retailers |
13. How Does Sustainability Play a Role in Pliers Manufacturing?
Sustainability is becoming an increasingly important consideration in manufacturing, including pliers production. As concerns about the environment grow, manufacturers are looking for ways to reduce waste, use eco-friendly materials, and minimize their carbon footprint.
What’s the real story? One of the main ways pliers manufacturers are becoming more sustainable is by using recycled or sustainable materials. Steel, a key component in pliers manufacturing, can often be sourced from recycled metal, which reduces the need for new mining and processing. This not only helps reduce the environmental impact but also cuts costs for manufacturers.
In addition to materials, sustainability also impacts manufacturing processes. For example, many manufacturers have switched to energy-efficient machines that reduce electricity consumption during production. Some companies are even adopting renewable energy sources to power their operations, further minimizing their environmental impact.
But here’s the kicker—plumbers, electricians, and other professionals are increasingly asking for tools that align with their sustainability values. As a result, pliers manufacturers are adapting their product lines to meet this demand, offering eco-friendly options and reducing the use of harmful chemicals and coatings.
Ready for the good part? As sustainability becomes more critical to both manufacturers and consumers, expect pliers production to evolve even further with greener practices and products.
Sustainability Factor | Description | Example |
---|---|---|
Recycled Materials | Using recycled steel and other metals | Eco-friendly pliers with recycled content |
Energy-Efficient Machines | Reducing electricity consumption in production | Solar-powered factories |
Eco-friendly Coatings | Using non-toxic or biodegradable coatings | Rust-resistant coatings with eco-friendly chemicals |
14. How Are Pliers Tested for Quality?
Quality control is an essential part of pliers manufacturing. To ensure that every pair of pliers meets the high standards required for safe and effective use, manufacturers perform a variety of tests.
What’s the kicker? These tests check the pliers for strength, durability, and functionality. One of the most common tests is applying pressure to the jaws to ensure they don’t break or deform under stress. Pliers must also be tested for cutting performance to ensure the edges are sharp enough to cut through wires or other materials without damage.
But here’s the real story—pliers are also tested for ergonomic performance. This means that the handles are checked to ensure they are comfortable and offer a good grip, even during extended use. Any sharp edges or rough spots on the handles are smoothed out to enhance user comfort and safety.
Ready for the good part? After the tests are complete, the pliers undergo a final inspection to ensure everything fits perfectly. The jaws, handles, and springs must all work together smoothly for the pliers to function properly. If any defect is found during the testing or inspection process, the pliers are sent back for corrections.
Test Type | Description | Purpose |
---|---|---|
Strength Test | Applying pressure to the pliers jaws | Ensures pliers can withstand pressure |
Cutting Performance | Testing the sharpness and cutting ability | Verifies effectiveness in cutting |
Ergonomic Test | Checking the handle comfort and grip | Ensures user comfort during use |
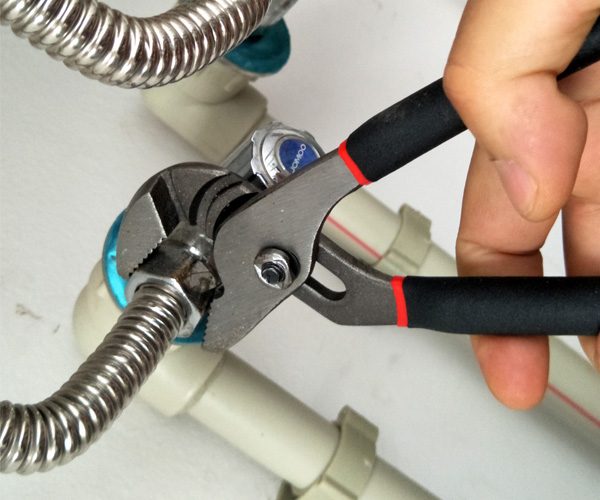
15. What Are the Latest Trends in Pliers Manufacturing?
Pliers manufacturing is not static—innovation and trends continue to shape the industry. New materials, technologies, and design features are constantly being introduced to improve the functionality and usability of pliers.
What’s the real story? One of the latest trends in pliers manufacturing is the integration of ergonomic features. As more professionals use pliers for extended periods, comfort becomes a major factor. Manufacturers are now designing pliers with padded, anti-slip handles to reduce hand fatigue and improve grip.
Additionally, the use of advanced coatings is gaining traction. Manufacturers are using diamond coatings and other high-performance materials to enhance the pliers’ longevity and reduce wear. These new coatings help protect the pliers from rust and corrosion, even in harsh environments.
But here’s the kicker—plumbers, electricians, and mechanics are increasingly relying on multi-functional pliers that can handle a wide variety of tasks. As a result, manufacturers are developing pliers with modular designs that allow users to switch out jaws or cutting heads for different applications.
Ready for the good part? These trends are not only making pliers more durable and versatile but also contributing to a greener, more sustainable manufacturing process.
Trend | Description | Example |
---|---|---|
Ergonomic Design | More comfortable, non-slip handles | Pliers with padded handles |
Advanced Coatings | Using high-performance coatings | Diamond-coated pliers for durability |
Multi-functional Pliers | Pliers with interchangeable parts | Modular pliers for various tasks |
Conclusion
Pliers manufacturing is a detailed and complex process, from material selection to final product testing. By understanding the materials, design, and manufacturing techniques used to create these versatile tools, you can better appreciate the quality and craftsmanship that goes into each pair. Whether you’re a professional using pliers in your daily tasks or a business in need of durable tools, knowing what goes into the manufacturing process can help you make better purchasing decisions. As trends evolve and sustainability becomes more important, expect pliers manufacturing to continue adapting to meet the demands of today’s markets.
FAQ
Q1: What is the pliers manufacturing process?
The pliers manufacturing process involves several stages, including material selection, shaping, heat treatment, coating, and assembly. The final product is rigorously tested for strength, durability, and functionality.
Q2: How does the heat treatment process enhance pliers?
Heat treatment strengthens the steel used in pliers, improving its hardness and resistance to wear. This process ensures that the pliers can handle tough tasks without losing their edge.
Q3: What materials are commonly used in pliers manufacturing?
High-carbon steel and stainless steel are commonly used in pliers manufacturing, offering strength and corrosion resistance. Plastic or rubber is used for the handles to improve comfort and grip.
Q4: How do I choose the right pliers for my project?
When choosing pliers, consider the type of work you’ll be doing, the size of the tool, and the grip comfort. Different pliers are designed for specific tasks, such as cutting, gripping, or working in tight spaces.
Q5: What is OEM, and how does it relate to pliers manufacturing?
OEM stands for Original Equipment Manufacturer. It refers to the production of custom tools designed to meet specific customer needs, including custom pliers for niche industries or branding purposes.